Industry 4.0
What is Industry 4.0?
Everyone in the manufacturing industry has probably heard of Industry 4.0. However, we are not always able to define this concept. The term itself, defining the fourth industrial revolution (originally Industrie 4.0), comes from the project of the German government's high technology strategy and was first used in 2011 during the international Hannover Messe fair.
Industry 4.0 is a generalizing concept describing the process of technological and organizational transformation of manufacturing enterprises, which includes the integration of intelligent machines, systems and ways of introducing changes in production processes to achieve even better efficiency. Industry 4.0 integrates people and digitally controlled machines with the Internet and modern information technologies. Materials used in production or produced become identifiable and easy to locate (traceability). The integration of machines and systems and the connection to the Internet create new communication possibilities. The flow of information takes place both vertically (from individual network components to central IT units and from IT units to components) and horizontally (between machines involved in the production process and the company's production system).
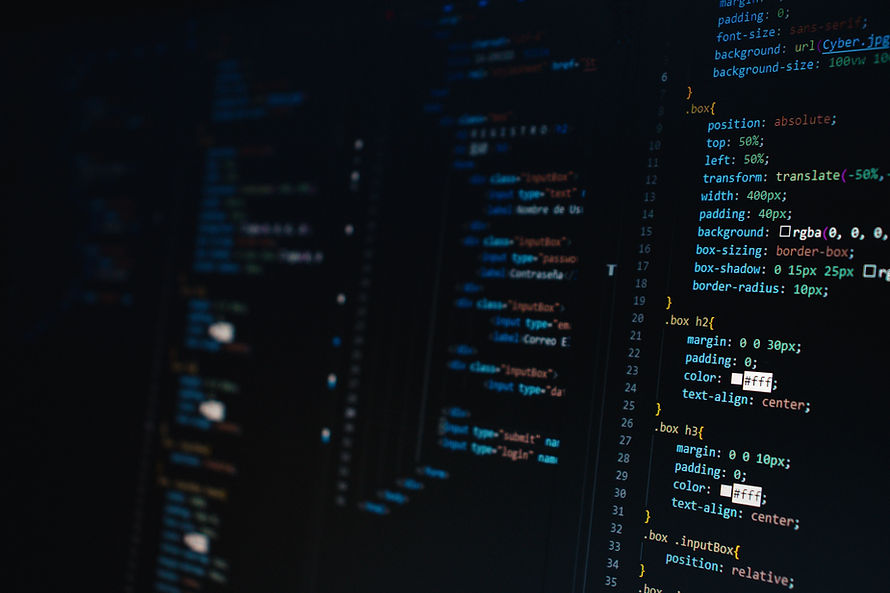