Our Success Stories
KepServer EXpert
Our company is a recognized expert in implementing, maintaining, and optimizing KepServerEx solutions across various industries, including automotive, pharmaceuticals, FMCG, and tobacco. We have successfully completed numerous projects, not only implementing Kepware but also enhancing and troubleshooting existing installations to meet the evolving needs of our clients.
KepServerEx is one of the most widely used and powerful tools in the IoT market. However, we have often seen companies overspend on features that are either underutilized or not needed at all. Our team specializes in optimizing budgets and designing efficient, tailored architectures that maximize the value of Kepware while minimizing unnecessary costs.
For legacy devices or older machines lacking existing plugins, we have provided seamless solutions using Kepware or ETL tools, ensuring full connectivity with modern IoT platforms. In cases where KepServerEx experiences instability, causing data gaps, delays, or missing information, we have swiftly identified and resolved these issues to restore permanent reliability and performance.
If clients are unsure about how to design their data architecture, which components to choose for maximum stability, or how to avoid safety gaps and excessive costs, we have guided them through the process. Our team has built robust, cost-effective architecture layers specifically tailored to the unique needs of each industry, ensuring optimal performance and long-term sustainability.
Design and implementation of an enterprise IT/IoT architecture
The customer, operating in the pharmaceutical industry, aimed to establish an effective, efficient, scalable, and secure digital environment for all five of its affiliates. This environment integrated core systems such as ERP, WMS, MES, and APS, along with platforms, production shopfloor equipment, laboratory and production devices, and sensors into a unified ecosystem. The solution ensured scalable and secure data exchange across all connected components, meeting the stringent regulatory and operational requirements of the pharmaceutical sector. The entire project was successfully completed within six months.

MES system implementation and customization
Over the past five years, we have been implementing MES systems for the automotive and FMCG industries, each project tailored to the unique needs of the client. The implementation of new IT systems presents an excellent opportunity to review internal business processes. Engaging a team with domain expertise allows organizations to identify potential improvements and set a clear direction for achieving tangible benefits. Prior to seeking external support, the customer lacked the internal resources to address this challenge. Following the successful implementation, a local team has been established and equipped with the necessary knowledge for system administration.
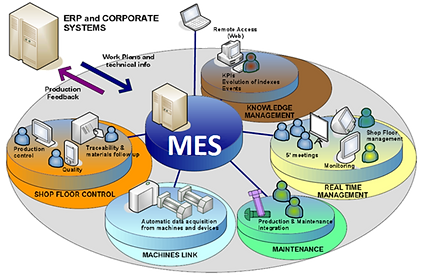
In-house MES System Creation
We have developed a scalable, modular MES system designed to adapt to the specific needs of each customer. The system consists of 14 independent modules, allowing businesses to select only the functionalities they require without the need to implement the entire solution. This flexibility ensures a cost-effective and tailored approach, enabling companies to optimize production processes without unnecessary complexity.
Our MES system supports key manufacturing operations, including real-time production monitoring, quality control, traceability, maintenance management, and seamless integration with ERP and shop floor equipment. The modular architecture allows for gradual expansion as business needs evolve, ensuring long-term scalability and adaptability to industry changes.

Creation a fully automate OEE calculation and live presentation.
Customer from the FMCG industry wanted to see real-time production data online, with main production KPIs like OEE, accessible via a web platform. The OEE platform is connected to MES and ERP systems to provide accurate and seamless data integration. The project, which lasted 7 months, focused on delivering a fully automated and efficient solution for live production monitoring.

Incoming goods delivery control
This case arose from a complaint made by the client's customer. For the FMCG client, we successfully completed the project within 3 months, delivering both business and IT solutions, along with all their components. Each incoming goods delivery of the specified materials was directed to quarantine before being released for production. Three independent platforms were integrated to operate seamlessly within a single ecosystem: the incoming delivery registration system, LIMS, and the machines/devices platform.

Product auto classification AI

Creation of an AI engine that helps the laboratory manager with product classification. We developed a fully automated algorithm that replaces the manual classification process, saving significant time. The AI engine also automatically inserts the required data into the laboratory controls in the LIMS system. This solution saves the Laboratory Manager 1.5 months of time yearly , improving efficiency and accuracy.
BI implementation + Business Analytics
The replacement of outdated static reports and Excel spreadsheets with fully dynamic, scalable BI dashboards is a common challenge many businesses face. At i4, we have already implemented several solutions in this area for different clients. These dashboards not only provide exactly what is needed but also offer the ability to integrate multiple external data sources and present information in a unified view, enhanced by dynamic filtering capabilities. Our solutions have helped clients streamline their business analytics and make more informed decisions.

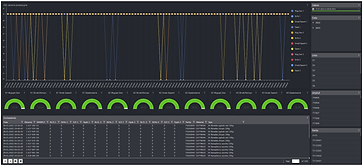
Production Process Online Visualization


Production Process Online Visualization is a critical aspect of modern manufacturing, applicable across all industries. At i4, we have implemented this solution in multiple sectors, helping businesses gain real-time insights into their production processes. Our solutions allow real production data to be displayed on TV screens above each machine on the Production ShopFloor, ensuring operators and managers can easily monitor performance. Additionally, we provide a historian feature for the production data, allowing Production ShopFloor Management to analyze historical trends and make data-driven decisions for continuous improvement. This approach not only boosts efficiency but also enables proactive management of production activities.
Energy Monitoring System
For our clients, we have implemented Energy Management System (EMS) projects that focus on optimizing energy usage and reducing costs. An EMS is a system that allows companies to monitor, control, and optimize their energy consumption by identifying inefficiencies and implementing strategies for energy savings. By deploying such solutions, our clients gained complete control over their energy resources, resulting in significant reductions in operational costs and supporting sustainability goals. This approach enables data-driven decision-making and drives energy efficiency improvements across organizations.



Production Process Control and Execution System
In today's fast-paced manufacturing environments, having a comprehensive system that not only visualizes production processes but also enables active control and execution is crucial. Our Production Process Control and Execution System combines real-time process visualization with robust control and execution capabilities, allowing companies to manage and optimize their production operations from start to finish.
For one of our large clients in the energy sector, we successfully implemented this system, which integrates seamlessly with their existing infrastructure. The system offers real-time monitoring of production activities and provides operators with the ability to steer the process, make adjustments, and execute tasks directly from the platform. This level of control ensures operational efficiency, reduces downtime, and improves overall production quality.
By incorporating process visualization with hands-on control, the system empowers managers and operators to proactively manage production workflows, optimize resource utilization, and swiftly respond to any challenges. This solution has proven to be a game-changer for our clients, enabling them to streamline their operations and improve decision-making at every stage of the production process.


System/platform/DB integrator
Data warehouse/Data lake (big data)
Date modeling
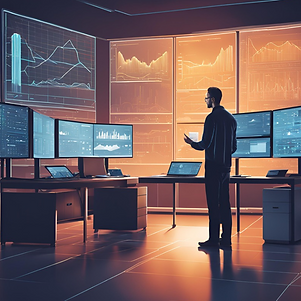
Our company has successfully completed numerous projects related to system, platform, and database integration for clients across a variety of industries. In many cases, businesses needed data that was dispersed across multiple platforms, systems, and servers. Extracting and consolidating this data, such as exporting it to Excel and preparing it manually, was often time-consuming and inefficient.
To address these challenges, we implemented solutions that established centralized sources of truth (Data Warehouse/Data Lake), enabling businesses to quickly and reliably access the data they required. In the projects we delivered, we also integrated BI layers that allowed the creation of dynamic, user-friendly dashboards with advanced filtering capabilities, eliminating the need for manual Excel exports.
Moreover, all data was structured within specialized data models, ensuring standardization, consistency, and governance across all factories and locations. These solutions have already supported our clients in achieving better data management, operational efficiency, and strategic decision-making.
To address these challenges, we implemented solutions that established centralized sources of truth (Data Warehouse/Data Lake), enabling businesses to quickly and reliably access the data they required. In the projects we delivered, we also integrated BI layers that allowed the creation of dynamic, user-friendly dashboards with advanced filtering capabilities, eliminating the need for manual Excel exports.
Moreover, all data was structured within specialized data models, ensuring standardization, consistency, and governance across all factories and locations. These solutions have already supported our clients in achieving better data management, operational efficiency, and strategic decision-making.
Obsolete/non-compatible devices with the IoT architecture
Our company has successfully tackled the challenge of connecting outdated machines, devices, and equipment to modern IoT platforms, demonstrating our expertise in solving unique integration problems. We have worked with companies struggling with legacy machines and equipment that could not support modern communication protocol stacks, often leading to the need for costly replacements.
Instead of pushing for unnecessary replacements, we helped our clients extend the life of their existing equipment. By leveraging IoT solutions, we enabled them to avoid replacement costs while maximizing the value of machines that were still in good technical condition. Each project was approached individually, with our specialists finding effective solutions to integrate legacy equipment with modern IoT systems, ensuring that IoT was not a trigger for equipment replacement but rather a tool to enhance its functionality.
Our successful implementations have allowed companies to maintain and optimize their operations while harnessing the potential of IoT—without the need for drastic equipment upgrades.
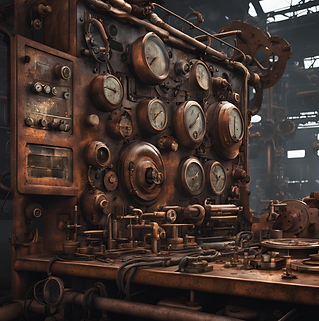
Iconics
Efektywne zarządzanie danymi i automatyzacja procesów to klucz do zwiększenia wydajności oraz redukcji kosztów. Jednym z naszych projektów było wdrożenie systemu ICONICS w zakładzie przemysłowym, które pozwoliło na pełne monitorowanie pracy maszyn i optymalizację produkcji.
Głównym celem naszego klienta było zwiększenie kontroli nad procesami produkcyjnymi poprzez zbieranie i analizę danych w czasie rzeczywistym. Klient poszukiwał rozwiązania, które:
- pozwoli na wizualizację kluczowych parametrów produkcji
- zautomatyzuje raportowanie i powiadamianie o nieprawidłowościach
- umożliwi zdalny dostęp do danych i analiz.
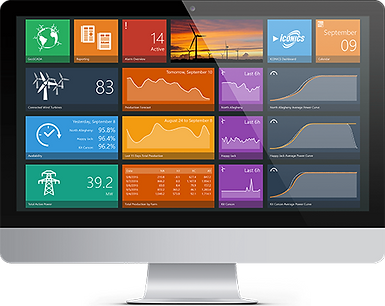
Machine Integration and Smaller Projects
Machine Integration and Smaller Projects
In addition to our expertise in KepServerEx and data architecture design, our company has also successfully delivered a wide range of machine integration and smaller tasks, using diverse technologies to meet the unique needs of each project.
We have extensive experience in direct communication with IT layers, enabling seamless interaction between machines and IT systems. Our team has also handled M2M (Machine-to-Machine) communication, ensuring secure and transparent data exchange between devices and systems. For older machines where standard communication options are not available, we have written custom communication drivers to overcome these limitations and ensure compatibility with modern systems.
Our integration projects have extended to laboratory and production control devices, where we have successfully connected these systems to IT platforms, enhancing the overall operational efficiency. Whether integrating new or legacy equipment, our solutions have consistently unlocked the full potential of manufacturing shop floors, ensuring smoother operations and better data flow.
In addition to large-scale integration tasks, we have also worked on smaller projects involving a variety of technologies, from PLC systems and SCADA to MES and OPC servers. Our team is skilled in a wide range of tools and technologies, including:
-
Kepware, OPC Servers, Iconics, ETL, Scripting (PS Batch), SQL, Grafana, BI (Qlik Sense, PowerBI, KPIWorX)
-
Zabbix, ELK, MQTT, OPC Router, HighByte, AWS, Crystal Reports
-
OPC UA, DA, ModBus
We have successfully applied these technologies to solve a variety of challenges, from real-time data monitoring and reporting to enhancing system interoperability and supporting data analytics for better decision-making. No matter the scale of the project, our team is committed to delivering reliable, tailored solutions that meet our clients' specific needs.